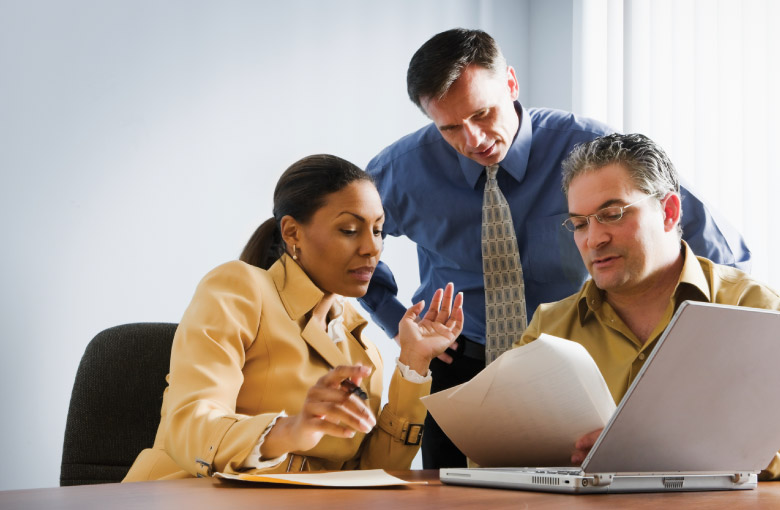
RFID technology gaining popularity with suppliers, retailers
Companies in the tech and pharmaceutical industries are increasingly adopting Radio Frequency Identification to track products from their manufacturing plants through the supply chain. Taking the first steps toward savvy use of RFID serves to both satisfy mandates from major customers (such as Wal-Mart and the U.S. Department of Defense), and boost internal supply chain efficiencies. Though the technology itself is still fairly immature, it is quickly winning hearts and minds among retailers and suppliers, according to Mark Barratt, a supply chain management professor at the W. P. Carey School of Business.
Mention RFID to anyone in the business community and they're likely to begin talking about Wal-Mart. The retail giant has been one of RFID's largest and most public proponents. Its infamous mandate –- which required its top 100 suppliers to begin using Radio Frequency Identification technology at the case and pallet level when sending product to three distribution centers in Texas by January 2005 -– sent suppliers into a compliance frenzy over the past few years.
But while Wal-Mart has received the lion's share of the hype involving RFID, it's not what is driving the most creative thinking about RFID –- nor what has the most potential to spur its future adoption. "Everyone is obsessed with Wal-Mart, but at the moment some of the more interesting developments for using RFID in the supply chain are happening outside of the grocery and consumer packaged goods industries," says Mark Barratt, assistant professor of supply chain management at the W. P. Carey School of Business.
Because consumer package goods companies –- which comprise a large portion of Wal-Mart's suppliers -- are beholden to consumer-friendly prices, the cost of RFID tags has prohibited the industry from truly embracing the radio frequency-powered tracking technology. Industries whose products are listed at higher price points -- such as defense, automotive, and pharmaceuticals –- are somewhat freer to experiment with RFID, says Barratt. "A $16 active RFID tag is next to nothing when your product sells for $1 million. In the grocery sector, a tag which costs 30 cents on a product that sells for $10 is a much less compelling argument," he explains.
RFID's overall popularity stems from its ability to help companies gain greater visibility into their supply chains. Long a buzzword in the logistics community, visibility of inventory location is crucial for tracking products as they move through the supply chain, from point of origin to final destination. Technologies such as RFID that provide this visibility help companies improve manufacturing processes, shipment accuracy and customer service, while decreasing costs and delays from distribution problems and inventory errors.
Defense industry steps up
The defense industry, in particular, has been proactive in adopting RFID, according to Barratt. "We are seeing more RFID creativity in the defense industry because they've got the freedom to do it; and they can pass some of the cost back to the U.S. Department of Defense," says Barratt. Because defense companies often produce the type of high-dollar items that can more easily absorb the cost of RFID tags, they have the potential to benefit much more from utilizing the technology.
The industry is also being pushed by the DoD's RFID mandate. In effect since Jan. 1, 2005, the mandate required suppliers of certain classes of products to tag shipments at the case and pallet level going to two of its supply locations: Susquehanna, Pa., and San Joaquin, Calif. By January of 2007, all DoD suppliers will need to use RFID at the unit level on all shipments to all DoD locations. While DoD's supply base doesn't extend as far as Wal-Mart's, the organization has certainly compelled many companies to invest in RFID initiatives.
DoD isn't simply playing "keeping up with the Joneses" with Wal-Mart. Effective supply chain management is crucial during combat situations, where getting the right product to the right place at the right time is about more than just keeping customers happy.
"The DoD can't have happen again what's happened in the recent Gulf war, where product was in the country, but not available to soldiers on the frontlines who needed it," says Barratt. Using RFID to track crucial supply elements can help eradicate those errors. The DoD is also trying to move toward a smaller, rapid-deployment type of force, and wants better certainty and visibility so it can reduce costs, Barratt explains.
Reactions to the DoD's mandate so far have been mixed.
"Some of the defense contractors have been very proactive with this," Barratt says. "Companies such as Boeing and Lockheed Martin have already shipped product with RFID tags; others have developed the capabilities, but haven't shipped any products; and others are waiting for orders that fall into those initial product categories that require tagging."
But complying with the DoD's mandate is only the starting point for defense companies taking the most forward-thinking attitudes about RFID. These companies are finding ways to use RFID to develop internal efficiencies –- the type of creative thinking necessary to truly spur widespread adoption, says Barratt, who has studied RFID use in a number of defense companies.
One DoD supplier Barratt worked with, for example, implemented an active RFID tag solution to tag the 4,000 to 5,000 pieces of test equipment used in its manufacturing location. The company has to test and calibrate its products fairly often before they are sent to the DoD, and as a result, employees were spending hours searching for the test equipment. By tagging the equipment with active tags, the company was easily able to find instruments it needed to test each of its products.
"The RFID application will pay for itself in the first 18 months, and in subsequent years, the company will save $300,000 to $500,000 in labor costs. It also reduced search time [for the test equipment] from approximately four hours to four or five minutes," says Barratt.
Other defense companies are using RFID applications to "track high-value components in their warehouses until they are needed for manufacturing" Barratt notes. From both an inventory and security point of view, this use of RFID has brought about internal efficiencies for defense companies. "They are using passive tags to track product location, and in doing so eliminating the need for manual cycle-counting, and they are using it to stop product from walking out the door," he explains.
Defense companies are also realizing internal benefits from RFID by gaining visibility of the manufacturing process. "When defense companies get a contract, they need to manufacture the product quickly –- the sooner they make it, the sooner they get paid," explains Barratt.
If suppliers are missing key components they need to manufacture a product, or they don't know what components they have, they'll have trouble meeting their customers' due dates. "Using RFID brings a benefit in terms of visibility and certainty during the manufacturing process," Barratt says.
But not all aerospace and defense companies have been so forward-thinking about RFID. Many are resistant to change, and steeped in a culture that is so contractually focused, says Barratt. Without a hard and fast contract that requires them to use RFID for a certain order, many companies are not moving ahead with deploying the technology.
"These companies say, 'Look at the contract we have with DoD; we know there's a mandate, but there is no contractual requirement for us to do this.' They live and die by the contract," says Barratt.
And suppliers feel the DoD hasn't been consistent with its demands regarding RFID. It has made two policy revisions since the original mandate, and does not have a consistent policy across its different branches.
"The Navy, Air Force, and Army are all coming up with different requirements," explains Barratt. "There is no real benefit for suppliers if they have to do things differently for different forces. Those extra costs are passed back to the DoD anyway, so that should be an incentive for them to get organized."
Ultimately for the defense industry, fully adopting RFID is more of a cultural challenge than one of price or technology. A willingness to try the new technology -– both for customer compliance and internal benefits –- has to break through. "This is going to take time. The industry is very slow moving," Barratt concludes.
Other early adopters
The pharmaceutical industry is another sector where RFID is gaining popularity, largely driven by government regulations aimed at cutting down drug thefts and counterfeiting. Barratt also sees big potential for industries that need to track containers through the global supply chain.
"From a global supply chain security aspect, there are plenty of applications for RFID," says Barratt. "We are already seeing some of the players in the 3PL [third-party logistics provider] industry doing this."
Large retailers are also piloting this use of RFID tracking, using the container data to comply with security regulations such as Customs Trade Partnership Against Terrorism (C-TPAT). Target, for example, has already piloted one program tagging containers, and using the data for security compliance, according to Barratt.
"By tying into C-TPAT, Target can take time out of the import process and reduce its lead times. Instead of needing three days for the documentation process, it can be done in less than an hour," he says. With congestion at ports still impacting shippers, getting in and out of customs quickly is a huge gain for retailers like Target.
Intel has also been very public about its initial RFID experiments. The company is using RFID to track large capital items in its manufacturing plants. "Intel is gaining several benefits from active RFID: better utilization of those tagged products, knowing where they are, saving time, and, from an auditing point of view, knowing what they actually have on hand," Barratt explains.
These companies -– along with the forward-thinkers in the defense segment -– have taken the first steps toward savvy use of RFID to both satisfy mandates from major customers such as Wal-Mart and the DoD, and boost internal supply chain efficiencies. Though the technology itself is still fairly immature, with common problems such as how to integrate RFID with existing internal systems, and where best to place tags and readers still being figured out, it is not going to fade away anytime soon, says Barratt.
What will it ultimately take for RFID to catch on in greater numbers? "If people are creative with it and if costs come down, you're going to see wide-scale application of RFID," Barratt predicts.
Latest news
- The surprising dynamics of CMO pay
New research reveals revenue risks of unequal C-suite compensation.
- Stay or go?
New research indicates that societal pressure can influence employees' decisions to leave their…
- Pioneering partnership brings essential software training to the public
A new certificate program from W. P.