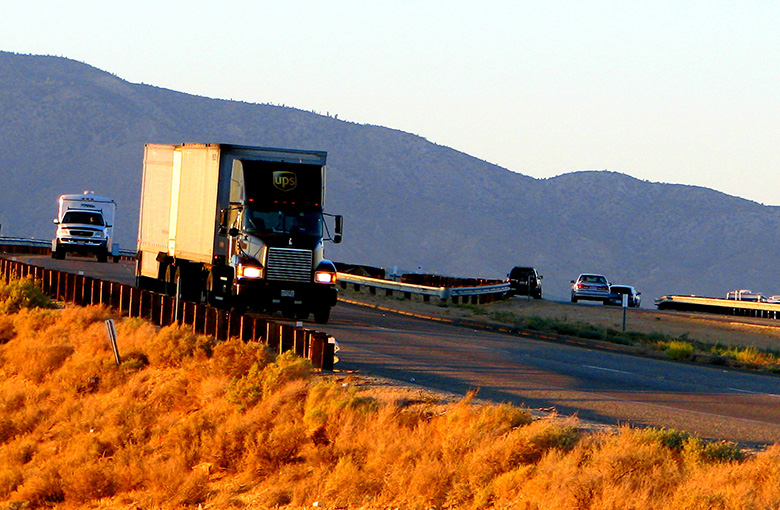
An analytical look at border crossing delays
Uncertainty is the enemy of the supply chain, and unfortunately that enemy is a constant companion of companies that maintain complex, extended, global supply chains. One factor in that uncertainty is the irregular nature of border-crossing delays, which W.P. Carey Supply Chain Management Professor Arnold Maltz is currently studying. Border-crossing delays are a reality for any company transporting products across a global supply chain, notes Maltz, who is researching ways to incorporate those delays into analytical inventory planning models.
Uncertainty is the enemy of the supply chain, and unfortunately, that enemy is a constant companion of companies that maintain complex, extended, global supply chains. One factor in that uncertainty is the irregular nature of border-crossing delays, which W.P. Carey Supply Chain Management Professor Arnold Maltz is currently studying.
Border-crossing delays are a reality for any company transporting products across a global supply chain, notes Maltz, who is researching ways to incorporate those delays into analytical inventory planning models. “Take the route from Vancouver to San Francisco,” he notes.“It’s probably 500 miles, and to make a 500-mile trip via truck within the United States takes about one to two days. But when goods travel 500 miles from Vancouver to San Francisco, if there are issues at the Canadian border, that trip could extend to three days. The problem is that you don’t know whether or not there will be a problem at the border.” As a result, businesses transporting goods across borders usually employ one of two strategies to combat the delay uncertainty: adding safety time or safety stock.
Companies may choose to add a day or two to quoted lead times for delivery, and/or keep an extra few days’ worth of inventory on hand. Neither are efficient or cost-effective. Safety stock, in particular, can add costs to the supply chain because companies are spending more to purchase and store the extra inventory, and they also run the risk of inventory obsolescence, Maltz says.
As such, obtaining a firmer grasp on how — and why — these uncertain delays impact the supply chain is key. “By definition, global supply chains involve crossing borders, so understanding how to include border crossings and border crossing activities in planning models is a significant concern for supply chain managers,” Maltz explains. Maltz’s quest to do just that has taken him through both empirical and analytical challenges. “I want to get a better handle on both sides of this issue. First, I would like to know what the delays really are; then, I want to get very specific about how to incorporate these delays in supply chain models,” he says.
Finding hard-to-find data
The first step has proved challenging. Collecting reliable and accurate data on border-crossing delays has been difficult, Maltz notes, in part because of the variability of the delays themselves. Anything from safety and security checks to congestion to misclassification or mistakes in Customs paperwork can cause slowdowns at borders. In addition, major events such as a terrorist attack or natural disaster may cause a crossing to shut down completely. “Or the delay could be as simple as something being labeled in the wrong language,” Maltz says.
Compounding the problem is that fact that Customs officials are the ones most likely to have data on border-crossing delays, and because of security concerns, they aren’t able to share the information with researchers. Instead, Maltz — with colleagues at other universities — is hoping to obtain data on the causes and frequencies of border-crossing delays from customs brokers and freight forwarders who often handle transportation for clients shipping goods around the globe. Just gathering the data, however, will not tell the whole story. “Even if we figure out, on average, how long it takes to cross a specific land border, there is still uncertainty. We still won’t know how often it takes three days to cross that border and how often it take three weeks,” he explains.
Factors like seasonality also contribute to the complexity. A company trying to ship goods from Mexico into the United States through Nogales, Arizona, in the winter months, for example, “will be in line with all the produce trucks,” Maltz notes. The border-crossing time at Nogales can vary from two hours normally, to up to a day-and-a-half in the busy season. “So, in that situation, would it make more sense for the company to use a different border crossing in January and February? It might; but it is hard to determine because no one really knows how often and how long the delays are there in the winter,” he says.
So, while the data-collecting issues are sorted out, Maltz has turned his attention to the analytical aspects of the problem. While on sabbatical in Boston, he has teamed up with researchers at schools including Boston University, Massachusetts Institute of Technology, and Brandeis University to help move the project forward.
Analyzing disturbances using control theory
The first question they must tackle from an analytical perspective, Maltz says, is figuring out what kind of disturbance the border adds to the supply chain. Historically, this question has been approached in the academic literature as a statistical issue.
Research has looked at what kind of standard deviation should be associated with these issues, and how that translates into inventory models that can determine how much inventory a business ought to carry in order to hedge for uncertainties. But Maltz wants to attack the problem from a different perspective. Borrowing from the engineering playbook, he plans to use a control theory approach as his framework. “Control theory says let’s look at what happens when you disturb the system, the flow,” he explains. “If the system is going along just fine, what happens if a delay or additional demand or something else is thrown in there? How does the system oscillate, and how long does it take to get back to a fairly steady state?” He is admittedly very early in his research process, but Maltz believes control theory can be helpful in studying the problem of border-crossing uncertainty because it is “an approach that should allow us to determine how much it is worth to have better information about how and why these disturbances impact the supply chain.” “We want to determine how valuable it is to have information — and to have it quickly — so if an unanticipated delay causes the supply chain to oscillate from its normal path, adjustments can be made to the supply chain,” Maltz says.
“Ultimately, the question is, how valuable is having that information versus keeping more inventory, versus putting money into the border so you are less likely to have these delays? This approach should give us models of how to balance all this out.” The quantitative models may be a ways away, but Maltz believes they will give companies another tool in their arsenal against the supply chain uncertainties associated with border-crossing delays. “I anticipate we are going to be able to say, ‘If you are bringing goods in through border-crossing X, you ought to assume there will be a certain amount of uncertainty and that uncertainty is likely to look like X. It could be a normal distribution — but probably not — and we suggest that for your inventory planning purposes, this is the set of equations you ought to be looking at,” Maltz explains; those equations will incorporate control theory perspectives.
The benefit for companies will be an improved ability to plan and change their inventory models in the face of disruptions and delays, and to make the necessary accommodations to ensure their supply chain still flows smoothly. If they have to increase lead time or inventory, for example, they should be able to tell what that lead time and/or inventory increase ought to be. “In some cases, you do safety time; in some cases you do safety stock; and sometimes you need both,” Maltz says. “I think we’ll be able to accommodate both of those things in the models, and that would be ideal.”
The models may also be timely because of tentative plans for a renewed U.S.-Mexico cross-border trucking program. If the pact is reinstated, it will allow Mexican truck drivers to operate in the United States, which could alter the current flows of U.S.-Mexico land-border crossings. This increased border freedom could also lead to an increase in “nearshoring” — or companies selecting Mexico as a sourcing or importing destination — which can also impact inventory planning scenarios. “Companies will want to examine questions like, Is it better to bring goods through a Mexican port? How much would it save in transportation costs compared with possible wage increases in Mexico versus Asian countries?, etc.,” Maltz says. “This control theory framework will be helpful for examining and modeling these types of issues as well.”
Latest news
- Buyers gain upper hand in Valley housing market
Arizona housing inventory is growing, but it's not yet a true buyer's market, says W. P.
- Wisdom from the supply chain OG
A W. P.
- MACC graduate Kailey Shupe finds immense value in program’s data analytics focus
The Master of Accountancy and Data Analytics (MACC) at W. P.