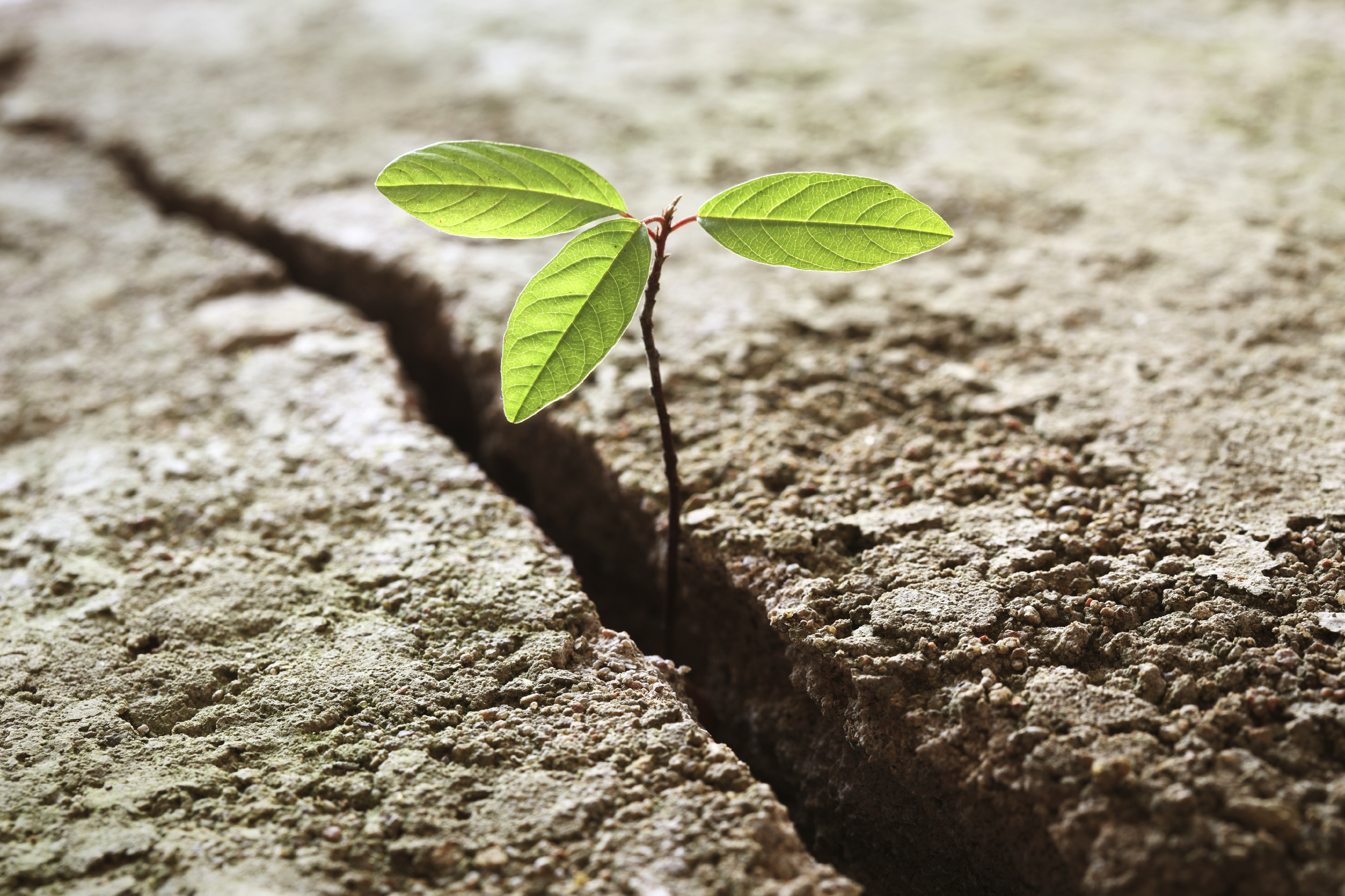
Expedited shipping, done environmentally
A case study on the green redesign of the U.S. Postal Service's expedited shipping products shows the importance of supplier collaboration in meeting sustainability requirements and keeping cost increases at bay. "One of the big issues with sustainability initiatives is cost, but the Postal Service was able to complete this green project and remain cost-neutral," says Phil Carter, a professor of supply chain management at the W. P. Carey School and executive director of CAPS Research. Private businesses can learn a lot from the Postal Service's example.
In many organizations, the desire for sustainable supply chains is outweighed by the need to reduce costs, or at least prevent costs from increasing. When a project can deliver both results — an environmentally friendly supply chain that is also cost-effective — it is a sure-fire winner. Such is the case with the U.S. Postal Service's (USPS) recent "green" redesign of its expedited packaging supply chain.
"One of the big issues with sustainability initiatives is cost, but the Postal Service was able to complete this green project and remain cost-neutral," says Philip Carter, a professor of supply chain management at the W. P. Carey School and executive director of CAPS Research, which recently documented the USPS project in its report, "The Greening of Expedited Packaging: A U.S. Postal Service and Supplier Collaboration."
"There are a lot of good lessons in this example," Carter says. "Private companies can learn that cost reduction is not the only way to achieve good results. It is better to be cost neutral than to do nothing, which is what many companies do when it comes to environmental projects, because they don't see the benefit." The USPS, however, clearly understands the benefits, and is committed to sustainability.
Its drive to become a more green organization stems from both an internal desire to be a responsible corporate citizen, and a sensitivity to the consumer perception that unwanted mail piles up in landfills and contributes to environmental problems, explains Susan Brownell, USPS vice president of supply management. In fact, the EPA estimates that mail makes up less than two percent of waste in landfills, she notes.
Among other things, the Postal Service's green redesign of expedited packaging was an important signal to consumers — and the marketplace — that it was embracing green principles. "We were trying, from a broader corporate view, to use the packaging changes to change the image of the Postal Service and show customers that we were committed to sustainability; that we were walking the walk and not just talking the talk," says Brownell.
Thinking About the Box
One part of the USPS' overall plan to "walk the walk" was to redesign its expedited packaging products — the boxes, envelopes, tubes and other containers and mailing supplies available to customers at Postal Service retail outlets and online. To do so, the USPS partnered with MBDC, a Charlottesville, Va.-based consultancy that helps companies revamp products and processes in accordance with its "cradle-to-cradle" philosophy, which aims to eliminate waste entirely.
Seeking help from a reputable firm like MBDC is a wise choice, notes Carter, because there is still a great deal of uncertainty around green initiatives. "Using a third party to bring a framework and some expertise in terms of green materials and chemicals is a good strategy," he notes. Together, the USPS and MBDC used the cradle-to-cradle protocol to assess the materials used in the expedited packaging products.
With some 200 suppliers of everything from paper products to inks and adhesives, as well as 1,400 ingredients to examine, the complex project took about two years. During that time, MBDC conducted supplier site visits to obtain product samples and ran tests to make sure the cradle-to-cradle requirements were met.
As a result of their efforts, the USPS made several important changes, including a reduction in the number of packaging types on offer. "We used to have separate packaging for international and domestic expedited shipping, and we decided to consolidate to one envelope type — a streamlined and greener process for us," notes Brownell.
The bulk of changes, however, were made to the inks and the adhesives used in the packaging products; small pigment changes in the ink, for instance, helped to meet MBDC's sustainability requirements, explains Joseph S. Han, contracting officer for the USPS. In addition, the expedited packaging redesign has netted an annual reduction of 15,000 metric tons of carbon emissions.
Don't Dictate; Collaborate
But while the results are significant, the collaborative process used by the USPS to work with its suppliers may be the most valuable takeaway, says Carter. Far too often when companies embark on process or product changes — green or otherwise — they make insulated decisions and merely dictate their demands to suppliers.
By contrast, the USPS worked closely with suppliers to "make tradeoffs, do collaborative research, and explore alternative solutions," says Brownell. "We could have taken a different approach and just said to suppliers, 'Here are the new specs,' but we took a collaborative approach, made the process an open dialog with our supply partners," she explains.
"That is a very important lesson," says Carter. "Working with suppliers to help solve problems rather than dictating one-sided solutions is key — and fairly unusual." Brownell also believes the USPS' history of collaborative supplier management played a role in the project's success. In some cases, she explains, suppliers were willing to absorb a cost increase instead of passing it along to the USPS because they decided that, as business partners, it was in their best interest to do so.
"We laid the groundwork over the years by adopting a partnering mentality with our suppliers. When you do that, suppliers see the value in the relationship and are willing to do things they might not normally do," she explains. Collaboration was also part of the reason the USPS achieved its cost-neutral status for this initiative. Taking the time to collaborate meant that the USPS could look to its suppliers to come up with alternatives if proposed solutions were deemed too expensive.
In one instance, MBDC's recommendation to make changes to the red ink on the expedited envelopes would have caused a significant cost increase. The USPS went back to its red ink supplier and together they found a way to make minor changes to the ink's pigmentation that would remain cost neutral. "Without that collaboration to look at alternatives, we would have incurred a significant cost," says Han.
Seeking Support from the Top
Not incurring those costs was, of course, an important goal for the USPS. Reducing costs or coming in cost-neutral was crucial in obtaining executive support for the project — a key factor in the project's success. Brownell points specifically to the top marketing executive as a major champion of the green makeover. "Our chief marketing officer was very committed to greening our products and she partnered with us in that process," Brownell says.
For example, as part of the redesign, the look of the expedited packaging materials received a major overhaul — from very colorful to a largely white design that was more reflective of an environmentally friendly product. "The purchasing group is not going to be able to push through that kind of change," Brownell says. "That has to come from the marketing side, and her support was very crucial in moving forward."
Garnering buy-in from top management is a must-do for companies looking to implement any type of sustainable supply management initiative, Carter notes. "Executive support is crucial. Supply managers often get caught in the middle — they'd like to go ahead with sustainability projects but they don't have the mandate to do so on their own," he explains.
The Bottom Line:
- One of the biggest deterrents to supply management sustainability projects is cost — but it doesn't have to be so. The U.S. Postal Service completed a successful greening of its expedited packaging products while remaining cost neutral.
- By working closely with suppliers, the USPS was able to find alternative materials that met sustainability requirements, and prevent cost increases. The project's cost-neutral outcome was key for gaining support from top Postal Service executives.
- The Postal Service adopted a "cradle-to-cradle" approach for this project, focusing on designing products that did not contain harmful materials and would not contribute to waste in landfills.
- The expedited packaging redesign was also geared toward boosting the Postal Service's image with consumers by appearing more environmentally friendly.
Latest news
- Flexible online master's of accountancy allows Natalie Goudarzian to continue career while leveling up
Programs like the Online Master of Accountancy and Data Analytics (Online MACC) from W. P.
- Tomato growers say looming duty on imports could upend business, raise prices
A W. P.
- Arizona and Mexico officials to meet for trade summit, address tariff concerns
ASU supply chain management expert calls Arizona-Mexico Summit a smart, strategic move for…